Metal Stamping Solutions
At Komaspec, we deliver superior metal stamping services, transforming your designs into high-quality metal components and products. Equipped with modern machinery and a team of highly skilled professionals, we ensure every part is stamped to your exact specifications. We work with a variety of materials, handle a broad range of thicknesses, utilize progressive and manual stamping dies, and offer an extensive range of secondary processes and surface finishing techniques. Below is an overview of our offerings:
Material
- • Aluminium (5052, 6061, 6063, 1060)
- • Carbon Steel (SPCC, HRS, SAPH440)
- • Stainless Steel (201, 304, 316)
- • Cold Galvanized Steel
Thickness
- • 0.1mm to 6.0mm
Stamping Dies
- • Regular Die
- • Progressive Die
Equipment
- • Stamping Presses: 16T, 25T, 40T, 63T, 80T, 160T, 200T
- • x 2 Material Auto-feeders
Secondary Processes
- • Assembly Services
- • TIG and MIG Welding
- • CNC Sheet Bending
- • Riveting
- • PEM
- • Laser Etching
- • Robotic Welding
- • Spot Welding
Surface Finishing
- • Powder Coating
- • Anodizing
- • Electro Coating
- • Trivalent Zinc Plating
- • Hot Dip Galvanized
- • Passivation
- • Geomet
- • Sandblasting
Why Choose Komaspec for Custom Metal Stamping
As a trusted provider of custom metal stamping, Komaspec is committed to delivering excellence at every stage of your project. Whether you're looking for complex parts or scalable production, Komaspec is well-equipped to handle all your metal stamping needs. Here's why Komaspec should be your first choice:
• In-House DFM and Tooling Design Expertise: At Komaspec, we manufacture all under one roof, providing greater supply chain control, transparency, better cost control, and shorter lead times.
• Material Versatility: We work with a range of materials including Aluminium, Carbon Steel, Stainless Steel, and Cold Galvanized Steel to suit your requirements.
• Scalable and Flexible Solutions: Our capabilities combine the scalability of a large enterprise with the flexibility of a medium-sized one, making us capable of handling projects of any scale and complexity.
• Vertical Integration: We integrate assembly with in-house component manufacturing for superior cost and quality control, providing you with reliable and cost-effective solutions.
• State-of-the-Art Stamping Facility: Our comprehensive stamping facility boasts a range of advanced machines, equipped to handle projects of any scale and complexity with utmost precision.
Contact Us
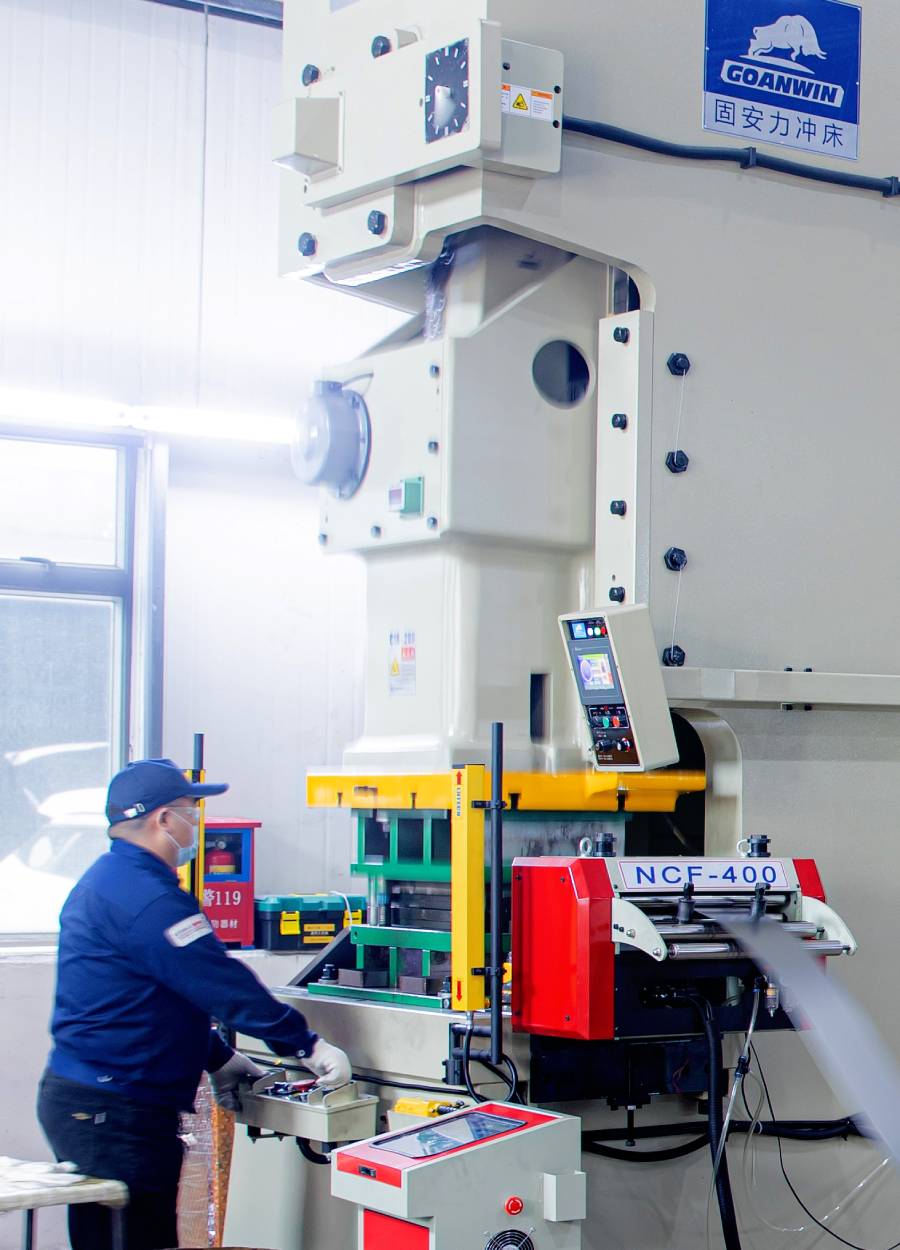

Progressive Stamping
Advantage
- • Lower stamping parts unit price
- • Higher accuracy with better part dimension repeatability
Disadvantage
- • Higher tooling investment compared to regular die stamping
- • Not all part geometries can be done with progressive stamping.

Regular Stamping
Advantage
- • Capable of doing any geometry of metal parts
- • Lower tooling investment
Disadvantage
- • Higher unit cost than progressive stamping parts
- • Lower accuracy with less repeatability
Manufacturing Solutions at Komaspec
Customized sheet metal fabrication services for medium to high volume orders.
Sheet Metal FabricationPipe and Tube processing for low to high volume orders.
Pipe and Tube ProcessingPrecision laser cutting and CNC bending manufacturing services.
Laser CuttingManufacturing and assembly for low to high volume orders.
Plastic InjectionStamping and progressive dies services for medium to high volume orders.
StampingVertically integrated for the fabrication of finished products.
Contract ManufacturingMetal Stamping FAQs
Progressive die stamping involves a single die that has multiple stages of operations, allowing the metal to progressively transform into the desired shape as it moves through the stages. This method is efficient and cost-effective for large volumes. On the other hand, regular die stamping, also known as single-stage or stage tooling, involves separate operations performed with separate dies. This method is often used for low volume productions or complex parts that can't be created with a progressive die.
Progressive stamping offers lower unit price and higher accuracy with better part dimension repeatability. However, it requires a higher tooling investment compared to regular die stamping, and not all part geometries can be done with progressive stamping. Regular stamping, on the other hand, is capable of doing any geometry of metal parts with lower tooling investment, but it has a higher unit cost than progressive stamping parts and lower accuracy with less repeatability.
Precision in stamped parts is ensured through the use of modern machinery and a team of highly skilled professionals. In addition, both progressive and regular stamping methods are used depending on the requirements of the part, ensuring high accuracy and repeatability.
Yes, Komaspec is able to handle your shipment for products manufactured by Komaspec. We have a network of freight forwarders whom we work with for shipments to various countries.
Should you need any references, please contact us at technicalsales@komaspec.com and we will be pleased to provide you with a reference list upon request.