Surface Finishing Options for Sheet Metal Parts
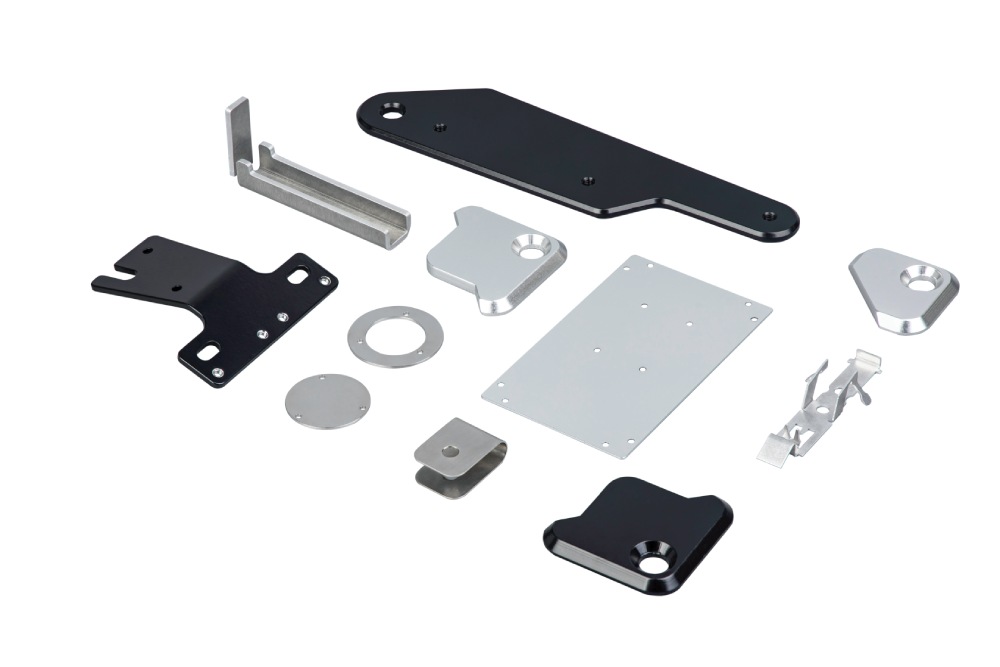
- Introduction
- What is Sheet Metal Surface Finishing?
- Why Add a Surface Finish to Sheet Metal Parts?
- What Metal Finishing Options are There?
- How to Select a Sheet Metal Finish
- Speak to a Metal Part Surface Finishing Expert at Komaspec
Table of Contents
Introduction
When designing or ordering sheet metal parts, it’s important to choose what kind of finish to apply to them. This is an underappreciated aspect of the design process, and choosing the right surface finish is more complex and has more implications than at first glance.
It’s important to choose the right surface finish for your sheet metal parts because it will impact the functionality, aesthetics and lifespan of the part. If a part is going to be subjected to constant mechanical wear, then this needs to be considered. If the part is to be used outdoors, then this too makes finish selection critical. The right finish is as important as the right dimensions: it’s a core aspect of what will make the part fit (or unfit) for purpose.
Actually choosing a finish, however, isn’t always that simple. To get things right, you need to know what properties you need to introduce in your part with the finish. Do you need a finish that will help it function properly or survive a tough environment? Is the part a customer-facing part on a designer product, and your top priority is something that will look great and fit your brand image? Considerations like these will influence the type of finish you should ultimately choose.
As well as considering what you need from your part, you also need to know what finishes are available, what benefits different finish types provide and when they can be used.
In this article, we’ll run through the basics to help you get started on choosing a finish for your sheet metal parts.
What is Sheet Metal Surface Finishing?
Surface finishing is one of the final stages in the manufacture of a sheet metal part. It is when the surface of a manufactured part is given a final alteration, and it is usually done for aesthetic reasons or to improve a part’s performance in use. It may also be done for both of these reasons, or for other reasons.
Surface finishing is often important. It’s particularly important for parts that need to look good or for parts that are subject to corrosion or large amounts of stress during use.
There are two basic ways in which surface finishing of a metal fabricated part is carried out:
- By adding a layer to the surface of a finished part.
- By removing material from the surface of a finished part or by reshaping it.
In this article, we’ll look at additive metal surface finishes. That’s finishes that are achieved by adding a layer of material to the surface of a sheet metal part. To find out about surface finishing processes that involve removing material or reshaping parts, you can review our article about mechanical / subtractive surface finishing for sheet metal parts.
Why Add a Surface Finish to Sheet Metal Parts?
As we’ve mentioned, the most common reasons for applying additive finishes to sheet metal parts are to improve either their appearance or functionality. In many cases, finishes are applied to achieve both of these aims.
Functional coatings are typically chosen to protect parts from corrosive elements in the environment or from physical damage that occurs during use. Aesthetic (appearance related) coatings are used to improve the look and texture of a part or for branding reasons.
It is less common, but coatings can also be used to impart certain physical properties on sheet metal parts or to aid manufacturing processes. Finishes may improve electrical conductivity or resistance, or chemical resistance, for example. Alternatively, they may be used to make welding easier during manufacture.
It's also worth mentioning that it’s not always necessary to finish a sheet metal part. Where parts are hidden or they aren’t exposed to an aggressive environment, it may not be necessary to carry out any surface finishing.
Aesthetic Reasons
Unfinished metal parts usually have aesthetic issues such as discoloration at cutting edges, burrs, abrasion marks on the surface or marks where vices have been used to hold them during manufacture. Adding a surface finish covers up these visual defects, improving the basic appearance of the part.
If parts are not finished, they will obviously also be presented as only the bare material from which they are made. Adding a surface finish, such as a layer of paint or powder coating, will completely change the color and texture of a part. This is particularly important for parts that are on visual display. A whole range of colors can be chosen with a finish as well as different textures, levels of light reflection or other visual properties.
Surface finishing may also be used for branding reasons. Brands that represent themselves through a particular color, such as John Deere, will use certain finish colors for branding reasons.
Durability
Parts that are subject to a harsh environment or stresses during use may be finished to increase their durability.
Parts that are subject to a great deal of wear from contact with other moving parts, for example, may be finished to increase their wear resistance. Anodizing is one type of finish that is used to increase wear resistance. During anodizing, an aluminum alloy is submerged in an acidic and electrolytic solution to create a wear resistant aluminum oxide finish.
Motor vehicle components, boat parts and sporting goods are all examples of products that are made with anodized aluminum parts. Other finishes can also be used to enhance durability, depending on the particular stresses or environment a part will be exposed to.
To Add Other Physical Characteristics
Surface finishes may also be applied to add other physical characteristics that improve the in-use performance of a sheet metal part. Surface finishes may also be added to increase the electrical conductivity or resistance of a part or to improve chemical resistance, for example.
Corrosion Resistance
Corrosion in metal is the breakdown of metal (through chemical or electrochemical reactions) into oxide, hydroxide, or sulfide. Rust is a well-known type of metal corrosion but is just one form that exists.
Surface finishes can be added to improve corrosion resistance. It is particularly important to add a corrosion resistant finish to sheet metal parts that are used outdoors or in other environments where corrosion is a serious issue.
Powder coating is an obvious example of a finish that increases corrosion resistance. By covering a sheet metal part in a powder coating, water and other substances that cause corrosion of metal cannot come into contact with the surface of the part. This prevents corrosion from being able to start.
Other finishes, such as anodizing and e-coating, also prevent corrosion. Careful selection is often needed, and it’s important to think carefully about what environment a part will be exposed to.
Galvanic Corrosion
Galvanic corrosion is a type of corrosion that it’s important to pay attention to with sheet metal parts. It occurs when two metals with different electrode potentials are submerged in an electrolyte and are electrically connected. This situation may sound unfamiliar, but its occurrence is actually quite common. A common example is when two connected metal boat parts are submerged in sea water.
Galvanic corrosion is an interesting process. When it occurs:
- One of the two connected metals will corrode at an accelerated rate.
- The other will corrode at a reduced rate.
As such, the process of galvanic corrosion causes the accelerated decay of one metal while it protects the other.
Fig. 1: Rusted Metal Surface
Galvanic corrosion is a significant risk for metal fabricated products where multiple metals are used and where parts are connected together. Fasteners are a good example. A fastener may cause a frame to corrode at an accelerated rate if the frame is made of a metal that has a different electrode potential.
Surface finishes can be used to prevent galvanic corrosion from occurring. By covering up metal parts that are at risk, it will not be allowed to take place.
Useful Galvanic Corrosion
Interestingly, however, galvanic corrosion can also be deliberately caused. With some metal products that are comprised two sheet metal parts, one metal part that corrodes more quickly is deliberately introduced in order to protect the other sheet metal part.
A good example of this is with zinc coated and galvanized dipped metal parts. If a zinc coating is applied to steel, the zinc will take on the sacrificial anode role and corrode first, protecting the steel it is coating.
To Aid in Manufacturing
Surface finishes may also be used to help during manufacture. Bead-blasting, for example, is often used because the texture it leaves on a part’s surface provides a ‘key’ for further painting or powder coating. Some surface finishes may also add chemical resistance, which may help during other manufacturing processes.
What Metal Finishing Options Are There?
This section outlines some of the most common choices of finish for sheet metal fabricated parts.
The list is not exhaustive, and there are other options available. Check with your custom fabricator to see what they offer and what they recommend for your specific needs.
Powder Coating
Fig. 2: Powder Coating
With powder coating, a dry powder (instead of traditional liquid paint) is electrostatically applied to the surface of a metal part. The part and its finish are then heat cured. With powder coating, the finished surface is harder and more durable than traditional paint.
Advantages:
- Durable and corrosion resistant.
- Finish is thicker and more uniform than with liquid paint.
- No drips or running, as is common with liquid paint.
- Can accommodate unique finishes, textures and custom colors.
- Fast curing time.
Disadvantages:
- Relatively expensive set-up costs.
- Part must be completely clean for powder to adhere properly.
- The best adhesion and performance against corrosion requires additional pre-treatment processing to remove rust, degreasing, surface activation and phosphating.
- Further treatment is required for saline environments.
Best Suited For:
Powder coating is best suited to sheet metal parts that are exposed to corrosion and that are also on visual display. The powder coating layer provides good protection from the elements and is also aesthetically appealing.
Typical Applications:
Powder coating is commonly used for: appliances, automotive components, outdoor equipment and furniture, outdoor signs, fencing, windows and doors.
Bead Blasting
Fig. 3: Bead Blasting
With bead blasting, special equipment that blasts thousands of tiny abrasive beads (usually glass or sand) at the surface of a sheet metal part is used to create a finish. The impact of these tiny beads creates a smooth surface finish with a slightly mottled texture. Defects such as burrs or discoloration are removed, and a more visually appealing and better textured finish is achieved.
Advantages:
- Creates a long-lasting finish.
- Many manufacturing facilities can perform bead blasting.
- Highly unreactive finish.
- Very useful when combined with other manufacturing processes.
Disadvantages:
- Time consuming process.
- Expensive for small production runs.
- Harder metals require more time for processing.
- Not suitable for parts with small dimensional discrepancy tolerances because small dimensional changes take place.
Best Suited For:
Bead blasting is often useful in preparing a sheet metal part for further manufacturing processes. It is particularly useful when a part will be painted or powder coated, for example, because the mottled surface finish it leaves aids in the adhesion of the paint or powder coating.
Typical Applications:
Typical applications are aircraft parts, guns and military equipment, automotive parts and medical products.
E-Coating
Fig. 4: E-coating
E-coating (electrophoretic painting) is a technique used to apply a thin coat of epoxy paint to a metal surface. A bath that includes paint with resins or pigments in a water-based solution is used along with an electric current to encourage coating particles to deposit on the metal surface. The coating is then cured with heat to complete the finish.
Advantages:
- Offers corrosion resistance.
- Can be used to increase surface thickness.
- Can be used as a primer for other finishing processes.
- Provides a more even coat than painting or powder coating.
- Finish has a consistent thickness.
- Good level of durability.
Disadvantages:
- May be a poor choice for cosmetic/visual parts.
- Needs another layer to be UV resistant.
- Needs to be combined with powder coating for the best levels of corrosion resistance.
Best Suited For:
E-coating is often used in combination with other finishing processes.
It’s a good choice for parts that have prolonged exposure to water, sun or outdoor environments and need to have a good level of corrosion resistance. It’s also a good option for parts that have hard-to-reach spaces, such as tubes or parts with interior surfaces.
Typical Applications:
E-coating is commonly used for: hardware, giftware, automotive parts, appliances, agricultural parts, marine components, metal furniture, outdoor furniture, outdoor tools and equipment and fixtures.
Anodizing
Fig. 5: Anodizing
With anodizing, an aluminum alloy is submerged in an acidic and electrolytic solution, and an aluminum oxide finish is created on its surface. While aluminum itself is corrosion and wear resistant, many of the metals used in aluminum alloys are not, and anodizing offers a way to compensate.
While it is most commonly used for aluminum and aluminum alloys, anodizing can also be used on nonferrous metals like titanium, magnesium, stainless steel, zinc and copper alloys.
Advantages:
- Improves hardness.
- Improves corrosion, abrasion and wear resistance.
- Gives a smooth finish.
- Dyes can be added to create a colored finish.
Disadvantages:
- With aluminum, only specific grades of aluminum can be used.
- Color variations can occur across a finished part.
- Expensive choice of finish.
Best Suited For:
Because it provides good wear resistance, this is a good option for parts that are in frequent contact with other materials. It is also commonly used for aluminum alloys exposed to saltwater or marine environments.
Typical Applications:
Typical applications are computer hardware, home appliances, building materials, marine parts (including ship hulls and docks), oil rig structures and components, roofing, construction materials and scientific instruments.
Zinc Coating
Fig. 6: Zinc Coating
Zinc coatings can be applied in two ways: by electrolysis or with acid zinc. Acid applications are faster but don’t always provide a uniform coating. Electroplating (electrolysis) is slower but gives a more uniform coating.
A fine zinc coating provides corrosion protection in two ways. Firstly, it provides a physical barrier on the surface of a metal part. Secondly, as a result of galvanic corrosion, it also acts as a sacrificial metal. In this case, it corrodes faster than the metal it’s connected to and reduces corrosion of that other metal.
Because of the way galvanic corrosion works, the protection a zinc coating provides will last even if the zinc surface covering incurs damage.
Advantages:
- Greatly improves corrosion resistance.
- Well suited to detailed surfaces.
- High strength finish.
- Finished metals have good formability.
- Can incur damage without becoming ineffective.
Disadvantages:
- Doesn’t suit use as an undercoat for other finishes due to reduced adhesion.
- Zinc coated parts cannot be welded. Welding should occur prior to coating.
- Limited to producing a bright colored finish.
Best Suited For:
Zinc coatings offer some of the best levels of protection against corrosion. Because corrosion resistance also continues after damage, they’re also useful in environments where damage is likely to occur.
Typical Applications:
Commonly used for: small parts (like nuts, bolts, and screws), automotive parts, military vehicles, wires and tubes, construction equipment and architectural parts.
Hot-Dip Galvanization
Fig. 7: Galvanized Sheet Metal Part
Galvanizing, or hot-dip galvanizing, involves submerging a metal part into molten zinc to create a very tightly bonded alloy coating. This is one of the most common ways to protect metal from corrosion damage. Like with zinc coating, the alloy coating provides both a physical barrier against corrosion and acts as a sacrificial anode.
Advantages:
- Improves corrosion resistance.
- Creates a uniform finish.
- Good resistance to mechanical or abrasion damage, and good durability.
- Good longevity of finish.
- Can adjust thickness of a finish.
- Fast application process.
Disadvantages:
- The thicker finishes create a rougher surface.
- There can be issues with weldability.
- Must start with a clean surface for proper bonding.
- May give a poor appearance.
Best Suited For:
Galvanizing is commonly used for heavy duty products where appearance is not critical. It’s also a more economical alternative to more costly corrosion resistant metal finishes.
Typical Applications:
Hot-dip galvanizing is commonly used for: automotive and machinery parts, construction materials, electrical boxes, electronic equipment, prefab buildings, HVAC parts, appliances, light fixtures, playgrounds and toolboxes.
Dacromet
Fig. 8: Dacromet
Dacromet is a finish product that combines zinc and aluminum flakes with a binder for cold-dipped or spray application. Heat is applied to complete the process. On completion, the product creates a finish by causing what is known as passivation on the surface of a metal part.
Advantages:
- High level of rust resistance.
- Provides complete barrier protection with a very thin layer.
- High level of temperature resistance.
- provides resistance to mechanical and chemical damage.
- Can be used to improve resistance to organics and salt.
- Creates an electrically conductive finish.
- Finish can be painted.
Disadvantages:
- Some Dacromet types may change metal mechanical properties.
- Resistance to mechanical damage is less than with other finishes.
- Not suitable for contact and connection with copper magnesium and stainless steel because contact corrosion will occur.
- Can be harmful to the environment and health.
Best Suited For:
Dacromet is best suited to stressed parts that will be exposed to heat and corrosion.
Typical Applications:
Dacromet is commonly used for: large automotive parts, nuts and fasteners, wind turbines, marine parts, agricultural and construction equipment and in aerospace applications.
Passivation
Fig. 9: Passivation
Passivation is the process of exposing stainless steel to an acid solution to remove free iron from the surface. The elements left behind change the reactivity of the metal’s surface to create a more rust and corrosion resistant finish. The finished metal surface is known as “passive” metal.
Advantages:
- Improves corrosion resistance.
- The process can be used for descaling or cleaning stainless steel.
- Can be a good follow-up procedure after welding, cutting or grinding.
Disadvantages:
- Metal must be cleaned well before passivation, or the process will be unsuccessful.
- Surface damage can result in corrosion.
- May need to be reapplied during the life of the part.
Best Suited For:
Passivation is best suited for preventing corrosion on surfaces that need to be kept clean.
Typical Applications:
Passivation is commonly used for: pharmaceutical equipment and food manufacturing equipment.
How to Select a Sheet Metal Finish
There are a number of important factors to consider when selecting a sheet metal finish and which will generally limit the number of viable choices.
- Material choice
- part application
- Part environmental conditions
- Tolerance requirements
- Cost Considerations
Here’s a quick run through of the main things you should consider.
Surface Finish & Material Compatibility
Not all finishes work with all sheet metal materials, so finishing options should be an important part of your material decision making process.
COLD ROLLED STEEL | HOT ROLLED STEEL | SPRING STEEL | ALUMINUM | STAINLESS STEEL | COLD GALVANIZED STEEL | |
---|---|---|---|---|---|---|
Powder coating | * | |||||
E-coating | ||||||
Zinc plating | ||||||
Dacromet | ** | |||||
Anodizing | ||||||
Passivation | ||||||
Hot Dipped Galvanized |
Table 1: Metal Surface Treatment Compatibility Chart
*Powder coating can be applied to cold galvanized steel, but special pre-treatment is required for the powder coating to adhere.
** Various types of Dacromet are available, including cold and hot processing types. Choose your type carefully to ensure the Dacromet surface finishing modifies the mechanical property of the underlying material correctly.
Part/Product Application
- Indoors vs outdoors – corrosion and other weathering process considerations (UV exposure, for example). Can the surface finish selected stand up to salt exposure (corrosion), will it color fade, etc.
- Aggressive environment – will a part be otherwise exposed to an aggressive environment? Will it be exposed to fumes or chemicals, for example?
- Visual display – if the part will be on visual display and its aesthetic appeal is important, it’s important to choose a finish that looks good. Texture will also be important in certain situations.
Part Design
- Is the part moving or stable? Certain finishes, such as zinc plating, can help to mitigate wear on moving parts. Other finishes, like powder coating, are much more vulnerable to wearing and flaking under mechanical stresses.
- Tolerance requirements – some processes, such as powder coating, have a larger built-in tolerance than others. Electroplating and anodizing in particular add very thin layers; for parts with high tolerance requirements these are generally a better option.
The table below summarizes how popular finishes perform in each of these areas.
Part Geometry
The type of part also plays a key part in the surface selection. Certain parts with complex geometry (e.g. tubes, pipes, folded enclosures) or sharp edges and folds, externally applied wet or powder paint will not evenly coat all areas of the part.
In this case, selecting a dip coating (like galvanization) or an electrical plating process (like e-coating), can ensure better coverage and even corrosion resistance.
For parts with outdoor applications or where corrosion resistance is crucial, this is often a key consideration. This is why many parts will combine e-coating with powder coating to ensure the entire product is protected against rust or corrosion.
Fig. 10: E-coated Sheet Metal Part
Combining Surface Finishes
Another common option is to combine two surface finishing options in order to get the advantages of each. Not all surface finishes can be combined, but
- Anodizing + Powder Coating – this is an usual but superior surface finish for aluminum parts which can achieve exceptional results.
- E-Coating + Powder Coating - this combination offers enhanced durability and corrosion resistance, creating a robust protective layer for a wide range of metal products.
- Primer + Surface coat of Powder Coating - this process ensures superior adhesion and added protection, resulting in a high-quality finish that enhances both the appearance and longevity of the coated item.
Surface Finishing Cost
Before deciding on a finish for your sheet metal parts, another essential step is to look into the cost and difficulty of achieving different finishes.
Some finishes cost more than others, and some will also add time and complication to the production process, and the cost is tightly related to the part size, complexity and weight.
Additionally, if multiple surface finishes are applied, the cost will be higher due to the greater amount of processing and the additional complexity and lower yield.
The best thing is to discuss the cost and difficulty of manufacturing with your manufacturer, but as a general rule of thumb, we’ve summarized the relative costs of these processes.
Process | Cost |
---|---|
Anodizing | $ |
Zinc Plating | $ |
Hot Dipped Galvanized | $$ |
Dacromet | $$ |
E-Coating | $ |
Passivation | $ |
Powder Coating | $$ |
E-Coating + Powder Coating | $$$ |
Dual Layer Powder Coating | $$$ |
Table 2: Sheet Metal Surface Finishing Cost Comparison Chart
Type | CORROSION RESISTANCE | COATING THICKNESS | ABRASION RESISTANCE |
---|---|---|---|
Powder coating |
|
|
|
E-coating |
|
|
|
Zinc plating |
|
|
|
Dacromet |
|
|
|
Anodizing |
|
|
|
Passivation |
|
|
|
Galvanized dipped |
|
|
|
Table 3: Metal Surface Finishing Properties Comparison Chart
Speak to a Metal Part Surface Finishing Expert at Komaspec
Our team of engineers and technicians here at Komaspec have more than 20 years’ experience in sheet metal fabrication in China. We’ll be glad to review your product design with you. We’ll also help you select the right surface finish for your parts and optimize your sheet metal and product fabrication strategy and design.
KOMASPEC'S SHEET METAL FINISHING EXPERTISE
Achieve the perfect finish for your sheet metal parts with Komaspec. Let us help you select the ideal finishing process for your project.