When to Use Progressive Die Stamping
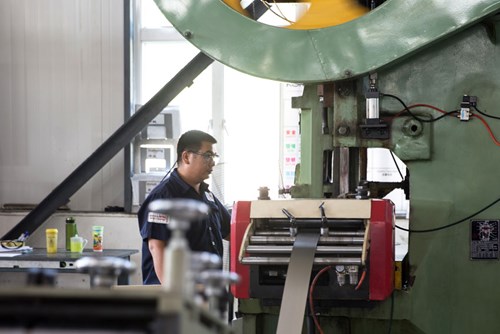
What is Progressive Stamping
In sheet metal fabrication, Progressive stamping is the process of choice for fabricating high volumes of complex sheet metal parts quickly and cost effectively. Progressive stamping is used for parts that require more than a single bend or punch.
Prior to the use of progressive stamping equipment, manufacturing a part requiring more than a single process was inefficient, required more than one pass through a machine, and added manual labor to move the part or change a die.
Progressive stamping equipment accomplishes this within a single process. The machine includes multiple stations, each equipped with a tool to perform a specific process on the part.
A strip of sheet metal is fed into the progressive stamping machine and continues to move horizontally through the different presses.
The part typically remains attached to the metal strip until the last press when it is cut.
The process can be very fast and potentially produce hundreds of parts per minute depending on the specifications.
Progressive stamping equipment uses a combination of dies and stamping presses to perform different techniques like punching, blanking, embossing, coining, bending, hemming, stretching, and flanging – all to achieve the desired shape of a piece. The process can use standard or custom dies.
Order and track sheet metal components online through Komaspec's on-demand sheet metal fabrication platform.
Advantages for high volume production
Progressive stamping creates a high volume of parts in a very short time. The shape of the part can be complex and include combinations of holes, bends, folds or other shapes while still being manufactured efficiently.
The short cycle times, and the high-quality, very repeatable process is hard to achieve with any other process or series of processes.
COST EFFICIENCIES
- Less manual labor required to manually change machines or tooling and fewer operators because fewer machines are in operation
- Eliminates the need for multiple setups, making setup faster and more cost effective per piece
- Minimal wasted scrap material
- Custom tooling may be required which can increase costs
- Less cost effective for short production runs
PRODUCTION SPEED
- The process involves a continual feed of sheet metal into the progressive stamping machine which works at very high speeds and allows for very long production runs
- Potential to fabricate hundreds of parts per minute
- Well suited to long production runs
- Eliminates the need to use multiple presses or change dies throughout the process
- Minimizes secondary machining processes
TOLERANCES AND PART DESIGNS
- Possible to create complex parts requiring multiple processes with tight tolerances all within a single process
- The process is highly repeatable resulting in less quality issues between parts
- Pilots and sensors are used to align the parts as they move from press to press to help ensure quality
- Less well suited to parts requiring deep drawing (the stamping depth is greater than the part diameter) or very intricate parts requiring very high degrees of precision
MATERIAL TYPE
- Can accommodate a variety of metals including:aluminum, steel, brass, copper, stainless steel, titanium and precious metals like silver, gold, and platinum
- Used by a wide variety of industries including electronics, appliances, food and beverage industries, retail, aerospace, home care
The team of engineers at Komaspec have more than 20-year experience in sheet metal fabrication and both progressive and standard stamping processes in our China-based sheet metal facility, and are glad to provide a product consultation and detailed DFM feedback to best optimize your stamping tooling and part design by reducing cost and improving output where possible.
We are glad to review your product design together and help you select the fabrication process that best suits your product’s needs.