How Material Properties Impact Air Bending Precision and Tolerances
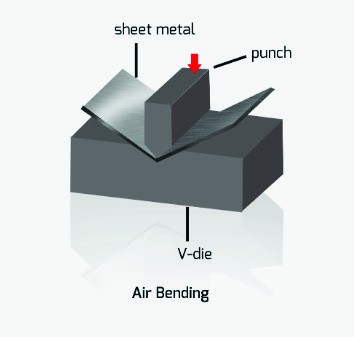
Bending Tolerances
Bending tolerances are a crucial part of your sheet metal fabrication. For parts requiring precision fabrication, be sure you understand what can impact those tolerance. Today’s bending equipment can be highly precise, however, the sheet metal itself presents the most significant challenge to achieving tight tolerances. In particular, air bending has some key considerations that impact bending tolerances:
- Material thickness
- Springback
- Direction of metal grain
- Material chemical and mechanical properties
Material Thickness
Variations in material thickness are one of the most common challenges when achieving bending tolerances. Sheet metal can have variations in thickness throughout a single sheet or between sheets. The nature of the rolling process often means sheets are thicker in the middle than the edges.
The gauge of different sheet metals is usually discussed with respect to averages, but in reality, the actual thickness can be anywhere within a specific range for that category. "A mere plus or minus 0.006 in. variation in material thickness can represent as much as 4 degrees of angular variation."
A very small variation in thickness can impact a bend angle by a few degrees. This has a big impact on results – especially when tight tolerances are required. Because with air bending, the bend angle is determined by width of the die and the depth of the punch, a variation in material thickness makes precision more challenging. If a narrow die is used, the impacts of inconsistent thickness is amplified.
Order and track sheet metal components online through Komaspec's on-demand sheet metal fabrication platform.
Springback
Springback is the “bounce” back of the metal after the press has been applied and removed. The sheet metal is compressed on the inside, where the press is applied, and stretched on the outside.
Because the material has a higher compression strength than tensile strength, it springs back towards its original shape. It is difficult to calculate springbackaccurately, but it needs to be considered when calculating the bend. Fabricators use the K-factor to calculate the springback factor and better understand how to compensate and achieve tighter tolerances.
The material’s plasticity is also a factor for springback. Plasticity is a measure of the material’s ability to deform without breaking and retain that shape. Higher plasticity metals are often better choices for forming and bending.
Several factors affect springback:
- Materials with higher tensile strength have more springback
- A sharp bend radius usually has less springback
- Wider die openings result in more springback
- The larger the bend radius relative to the material thickness the more the springback
Material | Tensile (MPA) |
---|---|
Cold Rolled Steel (CRS) | |
SPCC | ≥350 |
Hot Rolled Steel | |
#20 | ≥410 |
Q235 | 375 – 500 |
Q275 | 410 – 540 |
SAPH440 | ≥440 |
Q355 | 470 – 630 |
Spring Steel | |
65Mn | ≥980 |
Aluminum | |
AL1060 | ≥75 |
AL6061 T6 | ≥260 |
AL6063 T5 | ≥250 |
AL5052 H32 | 210 – 260 |
AL7075 T6 | ≥572 |
Stainless Steel | |
SS301 | ≥520 |
SS304 | ≥520 |
SS316 | ≥520 |
SS316L | ≥480 |
Cold Galvanized Steel | |
SGCC | ≥380 |
To eliminate the impact of springback when air bending, fabricators can overbend the part. In this case, the bend is done to a smaller angle to compensate for the anticipated springback.
Grain Direction
Fabricators should be aware of the sheet metal grain when choosing how to form a part. The grain is formed during the rolling process, with the grains running in a parallel direction to the rolling process. When forming or bending sheet metal with the grain (longitudinal), less force is required because the material is more ductile. However, longitudinal bends are best for a larger bend radius because the process can cause the grains to spread and produce cracks on the outside of the bend. Bending across the grain (transverse) requires more pressure but allows for a smaller radius with less risk of cracking on the outside of the bend.
Material Properties
Malleability is the ability to permanently press or deform a part without breaking or cracking.
Less malleable metals may require heat to achieve the desired effects.
Malleability | |
---|---|
6061 Aluminum | Difficult to bend and often cracks. Cold bending will weaken the metal. Annealing improves malleability. |
5052 Aluminum | Very malleable and good choice when using aluminum. Cracking is rare unless a part is reworked and. |
Annealed alloy steel | Varies based on the alloy. 4140 has good malleability. Annealing helps prevent cracking. |
Brass | Zinc content is important. Higher zinc levels make it less malleable. Good for simple bends but complex parts may require heat. |
Bronze | More difficult to bend and may require heat to avoid cracking. |
Copper | Very malleable. |
Cold rolled steel | Less malleable than hot rolled steel. |
Hot rolled steel | More malleable than cold rolled steel. |
Mild steel | Very malleable. Heat not required. |
Spring steel | Malleable when annealed. Once work hardened it requires heat to bend again. |
Stainless steel | Stainless steels like 304 and 430 are easier to form than 410 which can be brittle. Different grades will perform differently although stainless steel is prone to work hardneing |
Titanium | Strong material so best to design with a large internal bend radius. Overbending required because of springback. |
Strain Hardening
Air bending can cause strain hardening. Metal has a “yield point” and when strain is applied in the air bending process that reaches the yield point of the metal, it gets stronger and more force is required to bend it further. Strain hardening can pose problems in fabrication but can also be used to an advantage in producing strong parts. Materials like mild, low carbon steel and aluminum are more ductile and can be bent to a sharper radius without strain hardening.
Bendability
Bendability is an indication of the minimum bend radius, or the bend radius at which cracking of the outer surface occurs. It is often referred to in terms relative to the thickness of the material. Bendability can be reduced by rough edges as cracking can originate there. Material impurities or rough surfaces can also increase the likelihood of cracking and change the bendability. Using good quality materials and completing any necessary pre-bending processes can help minimize the impacts.
Overcoming Limitations
Fabricators can help minimize the material impact on precision bends with different techniques and tools:
- Measure and adjust - Fabricators program their CNC air bending equipment for a specific angle and will measure it once complete. If necessary, they can adjust the equipment and re-hit the part. This is only practical where few bends or parts are required.
- Over produce - If only a few parts are required, fabricators may choose to manufacture additional, measure the angle, and choose only those that are consistent or best. This is not feasible for large runs.
- Mechanical angle correction devices - Mechanical touch probes can be installed on CNC bending machines to move to the bend, measure it, trigger any necessary adjustment, and then move away again.
- Laser angle correction devices - Laser sensing technology can feed measurements to the CNC equipment to adjust for the desired angle. This technology minimizes disruption to the fabrication process and won’t add to the production time.
Our team of engineers and technicians here at Komaspec have more than 20-years’ experience in sheet metal fabrication in China and are glad to review your product design together and help you select the fabrication process that best suits your product’s needs, whether it’s laser cutting, bending, stamping, etc..
We are glad to review your product design together and help you select the fabrication process that best suits your product’s needs.