- Introduction
- What is Galvanic Corrosion?
- Damaging Galvanic Corrosion
- Protective Galvanizing
- Well-Known Cases of Galvanic Corrosion
- Why Does Galvanic Corrosion Happen?
- What are Dissimilar Metals?
- What is Meant By Electrical Contact Between Metals?
- Damage Caused By Galvanic Corrosion
- How to Prevent Galvanic Corrosion
- Choose Compatible Metals
- Fasteners Should Be Protected
- Consider Using Sacrificial Anodes
- Coatings and Non-Conductive Barriers
- Komaspec – Turnkey Solutions for Sheet Metal Products and Assemblies
Galvanic Corrosion: Why it Happens and How to Avoid It
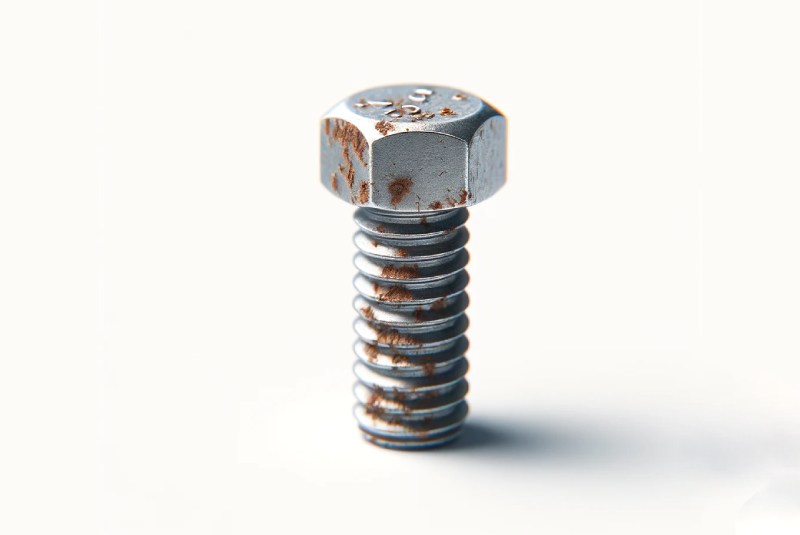
Table of Contents
- Introduction
- What is Galvanic Corrosion?
- Why Does Galvanic Corrosion Happen?
- Damage Caused By Galvanic Corrosion
- How to Prevent Galvanic Corrosion
- Choose Compatible Metals
- Fasteners Should Be Protected
- Consider Using Sacrificial Anodes
- Coatings and Non-Conductive Barriers
- Komaspec – Turnkey Solutions for Sheet Metal Products and Assemblies
Introduction
Galvanic corrosion can be an unforeseen cause of product, component or assembly failure. In some cases, it can even cause the failure of an entire structure or large piece of equipment.
Galvanic corrosion is a type of corrosion that affects metals, and it occurs as the result of an interesting chemical process. Predicting that it will occur is difficult without knowledge of the science behind it, and it often happens without people expecting it. Understanding the conditions in which it occurs, however, allows it to be avoided.
In many cases, it’s possible to avoid galvanic corrosion happening in the first place by only taking a few simple corrective steps. Furthermore, it’s also possible to use the process of galvanic corrosion to our advantage by using it to actually protect certain metals from corrosion.
In this article, we’ll explain what galvanic corrosion is in simple terms, why it occurs and what needs to be done in design to avoid the negative consequences. We’ll also run through some famous examples of galvanic corrosion to illustrate how serious a problem it can be.
What is Galvanic Corrosion?
Galvanic corrosion, also known as bimetallic corrosion, is a type of corrosion that affects metal. It occurs when two dissimilar metals are either in direct contact or electrically connected and immersed in an electrolyte. Dissimilar metals are metals that have different electrode potentials.
Galvanic corrosion is an electrochemical process that causes one metal to corrode in preference to another. When dissimilar metals are electrically connected within an electrolyte, the more reactive of the two metals will become an anode while the other becomes a cathode. The anode then corrodes at a rate that is much faster than when it is not coupled to the other metal. The metal that becomes the cathode also corrodes at a rate that is slower than when it is not coupled to the other metal. It is protected from corrosion, as a result. In some cases, corrosion of the cathode completely stops.
Galvanic corrosion can occur at different rates according to the level of difference between the two metals and the properties of the electrolyte they are immersed in. In some cases, it can be surprisingly rapid. It can also cause serious problems when it is not planned.
Damaging Galvanic Corrosion
Galvanic corrosion can be a serious problem when it isn’t expected or planned for. In structures, for example, galvanic corrosion can cause part of a structure to corrode at an unexpectedly fast rate. Where this happens to safety critical parts, this can be highly dangerous. In other instances, galvanic corrosion can just mean that equipment wears out much faster than expected. Otherwise, expensive repairs and replacements may be needed for metal components or entire pieces of equipment.
Fig. 1: Iron Beam Showing Signs of Corrosion
Protective Galvanizing
Because one metal is protected from corrosion through the process of galvanic corrosion, galvanizing is deliberately used as a protective measure. When a metal is galvanized with zinc or aluminum, for example, the galvanizing metal acts as a sacrificial material. It is allowed to corrode heavily in order to reduce corrosion of the metal that it protects.
Galvanic corrosion is also the process that is used to power wet-cell batteries. These commonly contain carbon-zinc cells, and the zinc corrodes in preference to carbon as part of the electricity production process.
Well-Known Cases of Galvanic Corrosion
Galvanic corrosion has caused problems for lots of engineers and other people. One area, however, where it might have caused the most problems is in shipping. Incorrect ship design that has resulted in galvanic corrosion being concentrated at certain points on ships has been a problem various times throughout history. Serious problems have occurred both before the process of galvanic corrosion was discovered and after.
The USS Independence
Galvanic corrosion caused serious problems recently in the USS Independence. This United States Navy ship is an aluminum hulled ship that was fitted with steel water jet propulsion systems in 2010. These steel systems became a cathode in the salty electrolyte sea water, with the aluminum hull becoming an anode. Corrosion of the hull occurred rapidly, and the problem cost millions of dollars to fix.
Lasagna Cells
One interesting example of when galvanic corrosion can occur at home is in what’s known as a lasagna cell. This occurs when lasagna is stored in a steel baking pan with an aluminum foil covering. The aluminum foil can corrode rapidly at spots where it contacts the lasagna. In this case, the lasagna becomes the electrolyte because it is salty, the aluminum foil is the anode, and the steel pan is the cathode.
Although, galvanic corrosion can cause serious problems when it occurs, it can be relatively easily avoided through good design. We’ll discuss design later in this article and explain ways in which this type of corrosion can be avoided.
Why Does Galvanic Corrosion Happen?
3 things are required for galvanic corrosion to occur:
- Two (or more) dissimilar metals
- An electrolyte solution
- Electrical contact between the metals
A common scenario, as we’ve mentioned, is with marine equipment in a saltwater environment. When salt dissolves in water, it releases electrolytes. Ions in the electrolytes are attracted to the electrons of nearby metals. If there are two electrically connected, dissimilar metals in the water, the electrolytes will be attracted to the electrons of the metal that is the cathode. In turn, this will start the process of galvanic corrosion as ions migrate between the sea water and the metals.
Fig. 2: Sheet Metal Part
What are Dissimilar Metals?
Dissimilar metals are metals that have different electrode potentials. If a material has a high electrode potential, it will lose electrons more easily than another material with a lower electrode potential. In galvanic corrosion, the metal with the higher electrode potential becomes the anode and corrodes faster than the other metal it is connected to (the cathode).
Corrosion occurs at an increased rate in the anode as a result of the ions in the electrolyte interacting with the two metals. Ions move between the electrolyte and the metals, and the anode releases ions and corrodes. Meanwhile, the cathode is charged with ions, hence why it is protected from corrosion.
What is Meant By Electrical Contact Between Metals?
For galvanic corrosion to occur, the two metals in question have to be electrically connected. This can happen if they are in direct contact or if there is something causing an effective electrical connection. Having an electrical connection facilitates the flow if ions between the two metals.
If two metal plates are bolted together, for example, they will obviously be in direct contact, which will create an electrical connection.
As well as the metals being electrically connected to each other, both of them must be immersed in the electrolyte solution to facilitate the flow of ions.
Damage Caused By Galvanic Corrosion
The damage caused by galvanic corrosion can be extensive and can even result in structural or component failure. When galvanic corrosion occurs, the anodic metal will fail much faster than expected in design.
Galvanic corrosion appears as rust or flaking of the surface of metal. Rusting of iron often happens as a result of galvanic corrosion.
Fig. 3: Rusted Metal Surface
A common example of component failure is when galvanic corrosion occurs between a metal fitting or fastener that is attached to a metal structure. If the fitting is made of a metal that is more reactive than the structure, it will become an anode and corrode at a fast rate. This often happens with screws that are used to attach a metal part to something else.
The Statue of Liberty
Another classic example of galvanic corrosion is the corrosion that occurred in the Statue of Liberty. As most people know, the Statue of Liberty gets its green color because it is made of copper. Copper commonly causes galvanic corrosion by acting as a cathode when in contact with other metals.
In the case of the Statue of Liberty, the copper statue was originally built on a cast iron frame. The frame was insulated from the statue to prevent galvanic corrosion, but the insulation failed, causing galvanic corrosion to affect the frame. Significant galvanic corrosion occurred, and very expensive repairs were eventually needed.
Repairs and improvements done in the 1980’s took two years and, while originally estimated at $103 million, they ended up costing much more. The most severe corrosion often occurs in situations like this where metals are in contact at joints or around fasteners.
- Example 1 – follow the link for an example of a mild steel and aluminum joint with significant corrosion and perforations in the aluminum after 2 years.
- Example 2 – follow the link here to see an example of brass and steel in contact.
How to Prevent Galvanic Corrosion
Galvanic corrosion can often be prevented through good design and planning. The best thing is to choose compatible metals, so the problem can be avoided altogether.
If that’s not possible, coatings and non-conductive barriers are an option.
Choose Compatible Metals
If it’s possible, the best thing is to choose metals that are compatible and less likely to create conditions favorable to galvanic corrosion.
There are two things to consider: their distance on the galvanic table, and their difference in the anodic index. Here’s the best basic approach:
- Choose similar, compatible metals whenever possible.
- Failing that, use metals that are as close to each other on the anodic index as possible (conditions dependent).
- If you have to use dissimilar metals, try to make the surface area of the anode larger than the cathode to slow corrosion.
Galvanic Tables
A galvanic table ranks metals based on their tendency to interact galvanically. Galvanic corrosion is more likely when metals are further apart on the table.
The galvanic table is meant as a guide as it doesn’t take into consideration other factors that might impact the corrosive potential of the metals. The table lists the most active anode metals first and the least active cathodes last. Different versions of the table are available for different environments or electrolyte solutions.
Included below is the table for low oxygen seawater.
Rank | Metal |
---|---|
1 | Graphite |
2 | Palladium |
3 | Platinum |
4 | Gold |
5 | Silver |
6 | Titanium |
7 | Stainless steel 316 (passive) |
8 | Stainless steel 304 (passive) |
9 | Silicon bronze |
10 | Stainless steel 316 (active) |
11 | Monel 400 |
12 | Phosphor bronze |
13 | Admiralty brass |
14 | Cupronickel |
15 | Molybdenum |
16 | Red brass |
17 | Brass plating |
18 | Yellow brass |
19 | Naval brass 464 |
20 | Uranium 8% Mo |
21 | Niobium 1% Zr |
22 | Tungsten |
23 | Tin |
24 | Lead |
25 | Stainless steel 304 (active) |
26 | Tantalum |
27 | Chromium plating |
28 | Nickel (passive) |
29 | Copper |
30 | Nickel (active) |
31 | Cast iron |
32 | Steel |
33 | Indium |
34 | Aluminum |
35 | Uranium (pure) |
36 | Cadmium |
37 | Beryllium |
38 | Zinc plating |
39 | Magnesium |
Table 1: Galvanic Series Table for Stagnant (Low Oxygen) Seawater
Anodic Indexes
Anodic indexes are another useful tool.
This anodic index shows the electro-chemical voltage between various metals and gold.
- In harsh environments with high humidity or saltwater, there should be no more than 0.15V difference between the metals.
- In less harsh environments without temperature or humidity controls, there should be no more than 0.25V difference between the metals.
- In temperature and humidity-controlled environments, a difference of 0.50V is possible.
Metal | Index (V) |
---|---|
Gold, Solid and Plated; Gold-Platinum Alloy | −0.00 |
Rhodium-Plated on Silver-Plated Copper | −0.05 |
Silver, Solid or Plated; Monel Metal; High Nickel-Copper Alloys | −0.15 |
Nickel, Solid or Plated; Titanium and Its Alloys; Monel | −0.30 |
Copper, Solid or Plated; Low Brasses or Bronzes; Silver Solder; German Silvery High Copper-Nickel Alloys; Nickel-Chromium Alloys | −0.35 |
Brass and Bronzes | −0.40 |
High Brasses and Bronzes | −0.45 |
18%-Chromium-Type Corrosion-Resistant Steels | −0.50 |
Chromium Plated; Tin Plated; 12%-Chromium-Type Corrosion-Resistant Steels | −0.60 |
Tin-Plate; Tin-Lead Solder | −0.65 |
Lead, Solid or Plated; High Lead Alloys | −0.70 |
2000 Series Wrought Aluminum | −0.75 |
Iron, Wrought, Gray, or Malleable; Low Alloy and Plain Carbon Steels | −0.85 |
Aluminum, Wrought Alloys Other Than 2000 Series Aluminum, Cast Alloys of the Silicon Type | −0.90 |
Aluminum, Cast Alloys (Other Than Silicon Type); Cadmium, Plated and Chromate | −0.95 |
Hot-Dip-Zinc Plate; Galvanized Steel | −1.20 |
Zinc, Wrought; Zinc-Base Die-Casting Alloys; Zinc Plated | −1.25 |
Magnesium and Magnesium-Base Alloys, Cast or Wrought | −1.75 |
Beryllium | −1.85 |
Table 2: Galvanic Voltage Compatibility Chart: Comparing Metals to Gold
Fasteners Should Be Protected
Fasteners are a common victim of galvanic corrosion. The fastener typically has a smaller surface area than the material it is fastening, so if the fastener is the anode, corrosion can be very rapid.
Fig. 4: Metal Screw With Sever Rust
To avoid issues, designers should consider the following guidance when planning a project or assembly:
- Whenever possible, use the same material for the fastener and the piece it is fastening.
- If using different materials, choose a fastener material that will be the cathode.
- Only use zinc coated fasteners on steel coated with aluminum, zinc, or galvalume.
- Do not use zinc or aluminum coated fasteners for copper or stainless steel.
This table can help with the selection of fasteners for a sheet metal fabrication project.
Base Metal | FASTENER METAL | |||||
---|---|---|---|---|---|---|
Zinc, Galvanized Steel | Aluminum and Aluminum Alloys | Steel and Cast Iron | Brasses, Copper, Bronzes, Monel | Stainless Steel Type 410 | Stainless Steel Type 302/304, 303, 305 | |
Zinc, Galvanized Steel | A | B | B | C | C | C |
Aluminum and Aluminum Alloys | A | A | B | C | Not Recommended | B |
Steel and Cast Iron | AD | A | A | C | C | B |
Teme (Lead Tin) Plated Steel | ADE | AE | AE | C | C | B |
Brasses, Copper, Bronzes, Monel | ADE | AE | AE | A | A | B |
Stainless Steel Type 430 | ADE | AE | AE | A | A | A |
Stainless Steel Type 302/304 | ADE | AE | AE | AE | A | A |
Key: | ||||||
A: Corrosion of the base metal is not increased by the fastener | ||||||
B: Corrosion of the base metal is marginally increased by the fastener | ||||||
C: Corrosion of the base metal may be marginally increased by the fastener material | ||||||
D: Plating on the fasteners is rapidly consumed, leaving the bare fastener metal | ||||||
E: Corrosion of the fastener is increased by the base metal |
Consider Using Sacrificial Anodes
One way to slow the process of galvanic corrosion is by intentionally introducing a highly active metal to act as a sacrificial anode.
The idea behind this is simple: the highly active metal will become an anode to the other metals that should be preserved. It will then corrode at a fast rate, while slowing corrosion in the metals that are being protected.
This method is simple and highly effective. The only issues are that cost may be prohibitive on large projects and the sacrificial anode will also need replacing periodically.
Coatings and Non-Conductive Barriers
Coating either or both metals can protect them from coming into contact with electrolytes, preventing galvanic corrosion from occurring.
This can work in 3 different ways:
- A metallic coating is used, which also acts as a sacrificial anode to protect the metal it is coating. Zinc coatings are commonly used for this.
- A non-metallic coating is used, which simply prevents the metals from coming into contact with the electrolyte.
- A non-conductive material separates the two metals, removing the electric connection between them.
Common coatings used to prevent galvanic corrosion include:
- Zinc plating
- Galvanized dipped metals
- Ecoating
- Powder coating
- Dacromet
- Anodizing
Design Guidelines for Coatings and Non-Conductive Barriers
- If only one metal can be coated it should be the cathode.
- The thickness of a coating is important if it is intended to act as a sacrificial anode.
- Common non-conductive insulators include polymer or elastomer-based bushings, washers, gaskets, or coatings.
- A non-conductive barrier must remain intact. Damage or degradation will lead to corrosion.
- A non-conductive barrier must break all contact between the metals in order to be effective.
Komaspec – Turnkey Solutions for Sheet Metal Products and Assemblies
Our team of engineers and technicians here at Komaspec have more than 20-years’ experience in sheet metal fabrication in China. We’ll be glad to review your product design together and help you select the fabrication process that best suits your product’s needs, whether it’s laser cutting, bending, stamping or something else.
If you need to prevent galvanic corrosion occurring in a completed assembly, we can also help. Our experts will be able to help you design out galvanic corrosion through correct material selection or the use of coatings, non-conductive barriers or sacrificial anodes.
ENSURE METAL PARTS DURABILITY WITH KOMASPEC
Maximize the lifespan of your metal components with Komaspec's advanced protection solutions.