Air Bending and Bottom Bending Sheet Metal
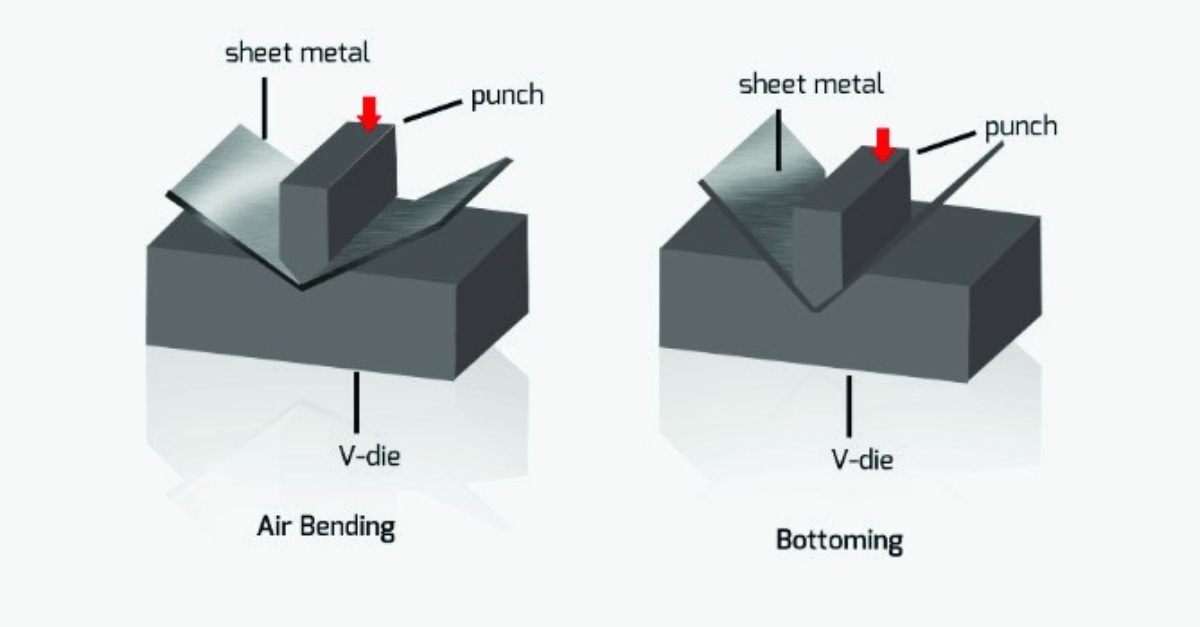
- What Are the Differences Between Air Bending and Bottom Bending?
- What is Air Bending?
- What is Bottom Bending?
- When to Use Air Bending
- When to Use Bottom Bending
- Sheet Metal Bending with Komaspec
Table of Contents
Air bending and bottom bending are two of the most common methods used to create bends during sheet metal fabrication. The names given to each method may sound unusual at first, but as you’ll see, both names actually describe each bending process perfectly.
In this article, we’ll explain how air bending and bottom bending work and when it’s best to use each method.
What Are the Differences Between Air Bending and Bottom Bending?
Air bending and bottom bending are both carried out using the same equipment: a die and punch. The difference between these two bending methods is down to the technique that’s used when a bend is created. Bottom bending is when the part is pressed full down to the bottom of a die (hence “bottom bending”) to form an angle. Air bending is when the part is pressed partially downward against a die to create a given angle. The part still has clearance between itself and the bottom of the die (“air bending” for the visible air between the two).
Fig. 1: Air and Bottom Bending (Skill-Lync)
Bottom bending can be used to create accurate, neat bends in metal parts that need a greater deal of precision. Air bending is slightly less accurate, but it’s faster and much more convenient in the production process.
Both bending processes can be performed using a manual or CNC controlled press brake. In general, more accurate press brakes will be needed for air bending. When it comes to bottom bending, however, accuracy in the press is less important, but more scrap may be generated. More equipment maintenance may also be needed for bottom bending as well due to the pressure exerted against the die and the impact on the hydraulics of the press brake.
Air bending | Bottom bending | |
---|---|---|
Custom Tooling |
Not required |
May be required |
Die / Radii |
Single die can accommodate multiple angle radii |
Unique die is required for each angle radius |
Angle Accuracy |
>± 45' |
±15-30' |
Best Used For |
Parts where bend accuracy isn't vital |
Parts where bend accuracy is important |
Pricing |
No tooling investment / higher part price |
Tooling investment / lower part price |
Table 1: Air Bending and Bottom Bending – a Quick Comparison
What is Air Bending?
Fig. 2: Air Bending
With air bending, a press brake is equipped with a punching tool, and this is used to apply pressure to a piece of sheet metal. A V-shaped bottom die is used beneath the punching tool to support the metal during the bending process. To create a bend in metal, the punch presses the material into the bottom die as far as is needed to achieve the correct bend angle.
Air bending is known as air bending because the sheet metal is not fully pressed into the die during bending. Instead, as in the image above, air is left between the sheet metal and the die. With air bending there are always only three contact points during bending: One on each side of the top of the V opening of the die and one at the tip of the punch.
Because the metal sheet isn’t pressed to the bottom of the die, the shape of the die does not define the angle of the bend. Instead, the depth to which the metal is pressed inside the die defines the angle of the bend.
With air bending, the same die can be used to accommodate a range of bend radii and bend angles. Any radii and angle that fits within the punch profile and depth is achievable. A range of materials can also be accommodated.
One common challenge with air bending is that bent pieces will experience more springback than with other bending methods. This is when the metal flexes back slightly towards its original shape after bending. Angles also aren’t quite as accurate as with bottom bending. One way to overcome the problems inherent to air bending is to use laser measuring technology that assists with accuracy.
Fig. 3: Overcoming Springback with Laser Technology
Air Bending Advantages
- No retooling or equipment changing is required to create different bend angles - saving time and expense in production
- Able to bend most material types and thicknesses
- Faster than bottom bending
- Less pressure is required to perform the bend
- Less contact with tooling results in less surface damage
Air Bending Disadvantages
- Not well suited to parts requiring highly accurate bend angles
- Material will have a springback effect which needs to be compensated for in the bend angle
- Using older press brake equipment often results in inaccurate bends
What is Bottom Bending?
Fig. 4: Bottom Bending
Bottom bending also uses a punch and V-shaped bottom die, just like air bending. What’s different is that the punch is used to push the metal fully into the die to create a bend. Bottom bending (or bottoming as it’s otherwise known) gets its name because the metal is forced to the bottom of the die. Higher pressures are used, and the metal comes into full contact with the punch and the die.
Because the material is pressed into the bottom of the die, the die that is used will determine the bend angle that’s achieved. With bottom bending, you have to change the die to achieve a different bend angle. This isn’t the case with air bending because the punch can just be pushed to a different depth in the die.
Bottom bending results in less springback and creates more accurate angles. The big disadvantage is that each new bend radius requires a different bottom die, which means swapping it manually on the machine. The machinery is also put under more pressure during production.
Bottom Bending Advantages
- More accurate angles than air bending
- Less springback than air bending
- Older, inaccurate presses can be used
Bottom Bending Disadvantages
- Unique tools are required for different bend angles – this means more tooling investment and more tooling changeovers
- Requires more pressure on the press brake than air bending
- Contact with punch and die can leave tooling marks on the part
- The process is slower because greater pressure is applied and a longer range of motion is required
When to Use Air Bending
Generally speaking, air bending is more suited to production runs where accuracy is less important and being able to produce parts quickly is beneficial. If you need to mass produce parts, make parts that vary in angle or save money in production, then air bending is usually best.
When Accuracy isn’t Vital
Air bending is appropriate where a high level of accuracy isn’t essential. With air bending, there’s usually a greater level of inaccuracy in bends and variation between pieces than there is with bottom bending. Bottom bending ensures accuracy because pressing a metal sheet into the shape of the die is more reliable. With air bending, variation occurs because of inaccuracy in the machinery, with variations of ±0.5° being possible.
Springback is also more of an issue with air bending, as we’ve already mentioned. This can be overcome to an extent by overbending the sheet metal in the first instance, but this method can have difficulty in predicting material variability and individual part behavior. However, better results are still achieved with bottom bending.
For Faster Production
Air bending is good for speedier production runs.
First of all, the process of completing an air bend is faster than the process of completing a bottom bend. The metal does not need to be fully pressed into the die, and less pressure and time is required to complete the bend.
It’s also possible to create multiple bend angles with the same die and press. Rather than changing the die, the punch just needs to be pressed into the die to a different depth to create a different bend angle. This saves set-up time because the die and press don’t need to be changed for new bend angles between each batch.
Reduced Costs and Easier Production
Other benefits that air bending offers are reduced costs and a reduction in the amount of part tooling and machinery maintenance that’s required. Air bending can also be used where the operator needs to have control over the bend angle during bending. It’s also useful where it’s beneficial to use less bending force on a particular material.
When to Use Bottom Bending
The main benefit that bottom bending brings is a much higher level of accuracy. This is a big benefit, but the production process is more difficult.
Greater Accuracy
Bottom bending creates reliable, accurate bends in sheet metal. Where accuracy in bend angles is important and variation between different parts in a production run needs to be avoided, bottom bending is preferable. Springback is also much reduced with bottom bending, and so it’s useful when this needs to be avoided. If you need to create accurate, more precise parts, bottom bending is usually the best choice.
Machine Flexibility
One situation where bottom bending is useful is in workshops where only an older more or less accurate press brake is available. While the press brake itself may lack the accuracy of a more modern machine, the die can help to compensate as the die is what is guaranteeing final bend angle, rather than the machine itself.
Comparison | Air Bending | Bottom Bending |
---|---|---|
Accuracy & Precision |
- Greater level of inaccuracy and variation between pieces. - Springback more prevalent, requiring overbending. - Not well suited for parts requiring highly accurate bend angles. |
- Ensures reliable, accurate bends in sheet metal. - Ideal for precise parts and consistent bend angles. - Less springback than air bending. - More accurate angles than air bending. |
Production Speed |
- Faster than bottom bending. - Able to bend most material types and thicknesses. - Less pressure required to perform the bend. |
- Slower compared to air bending due to full pressing into the die. - The process is slower because greater pressure is applied and a longer range of motion is required. |
Flexibility & Cost |
- No retooling or equipment changing needed for different bend angles. - Less contact with tooling results in less surface damage. - Using older press brake equipment often results in inaccurate bends. - More control over bend angle during bending. |
- Unique tools are required for different bend angles – means more tooling investment and changeovers. - Requires more pressure on the press brake than air bending. - Contact with punch and die can leave tooling marks on the part. - Older, inaccurate presses can be used. |
Table 2: Comparative Analysis of Air Bending and Bottom Bending Techniques
Sheet Metal Bending with Komaspec
Our team of engineers and technicians here at Komaspec have more than 20 years’ experience in sheet metal fabrication in China. We’ll be glad to review your product design together with you, optimize sheet metal design and help you select the fabrication process that best suits your product’s needs, whether it’s air bending, bottom bending or a process like laser cutting or stamping.
KOMASPEC'S ADVANCED METAL BENDING SOLUTIONS
Boost your sheet metal projects with Komaspec's precise bending solutions—air or bottom bending tailored to your needs.